Engineers have many solutions available for managing their files and product information. Two key systems are Product Data Management (PDM) and Product Lifecycle Management (PLM). In general, PDM PLM systems help you manage files that you create when creating products. In fact, according to a study of over 2,500 responses by Tech Clarity, top performing manufacturers are 30% more likely to use PDM or PLM and spend 25% less time on nonproductive data management tasks .
Engineers use Product Data Management software during the product design phase. Product Data Management is tied with your Computer-Aided Design (CAD) system. PDM helps you manage your product design files and assemblies.
Product Lifecycle Management software manages files created across the life of the product. The product lifecycle starts with an idea, to design, manufacturing, maintenance, and retirement. PLM software helps manage the information across each of these stages.
Here are 4 key differences between PDM and PLM. So you can distinguish the differences in types of problems they are trying to solve. With this information you can make more informed decisions in the PDM PLM buying process.
1. Size and Scope
PDM and PLM systems often differ in their size and scope. PLM systems tackle the entire process of the product. PDM systems focus on the engineering and design phase of the product life. Therefore, PLM systems have a broader application and a bigger scope.
.jpg?width=1200&height=800&name=PDM%20vs%20PLM%20(1).jpg)
PLM systems often include PDM software features. Be sure to identify what PDM features you are looking for and identify if those are included in a potential PLM system.
2. Process Integrations
Because PDM and PLM systems vary based on size and scope they might integrate to different apps. PDM systems are focused on the engineering and design stage, so might only integrate with your CAD system. PLM systems cover stages of the product life where files are created around the concept, managing invoicing, managing parts, and maintenance reports. PLM system might integrate with and Enterprise Resource Planning (ERP), billing, or Customer Relationship Management (CRM) system.
A PLM system allows you to keep all your files and information in the same place. This makes it easier to share files across phases and optimize the product creation process.
Consider what apps you want to integrate so you can store your files in the same place. If you want a broader integration list consider a PLM system. If you want to focus on your engineering design and CAD files, a PDM focus might be a better fit.
3. Purpose
PDM and PLM systems solve different problems.
PDM help optimize the engineering design process. You are making it more efficient to design and develop products. With a PDM, you are increasing the efficiency of the engineering design department.
PLM solves more widespread issues. Implementing a PLM helps when you want to optimize the entire process. Consider your entire companies process of developing a product. Are you experiencing challenges just in engineering design, or throughout the whole product creation process?
4. Budget
Because of size and scope, PLM systems tend to be more expensive than PDM systems. Although PLM and PDM systems are often one in the same, your use case can define how much budget you need.
If you are using a PDM PLM system to solve PLM problems, then you need to include more users throughout the product creation process. If you are using a PDM PLM system to solve PDM problems, then you only need to budget for users in the engineering and design department.
Also consider the cost of implementation. To use a software for PLM, you need more integrations, more user input, more testing, and more requirements. In some cases, there could be conflicting requirements. What if the sales and marketing team is on board with moving their files to a cloud model, but the engineering and design department is not yet ready? The wider the scope, the more people that need to be convinced and higher cost of integration.
PDM vs PLM Feature Comparison
PDM is focused on being an engineering productivity tool, while PLM is the broader process improvement tool. Let's compare the features.
PDM features are focused on helping the engineering team design faster and with more control over their designs. This includes document management, version control, and CAD data management.
PLM had a broader scope to improve the entire process the company uses to deliver a product to the customer. This include project management, supplier collaboration, change management, and product processes.
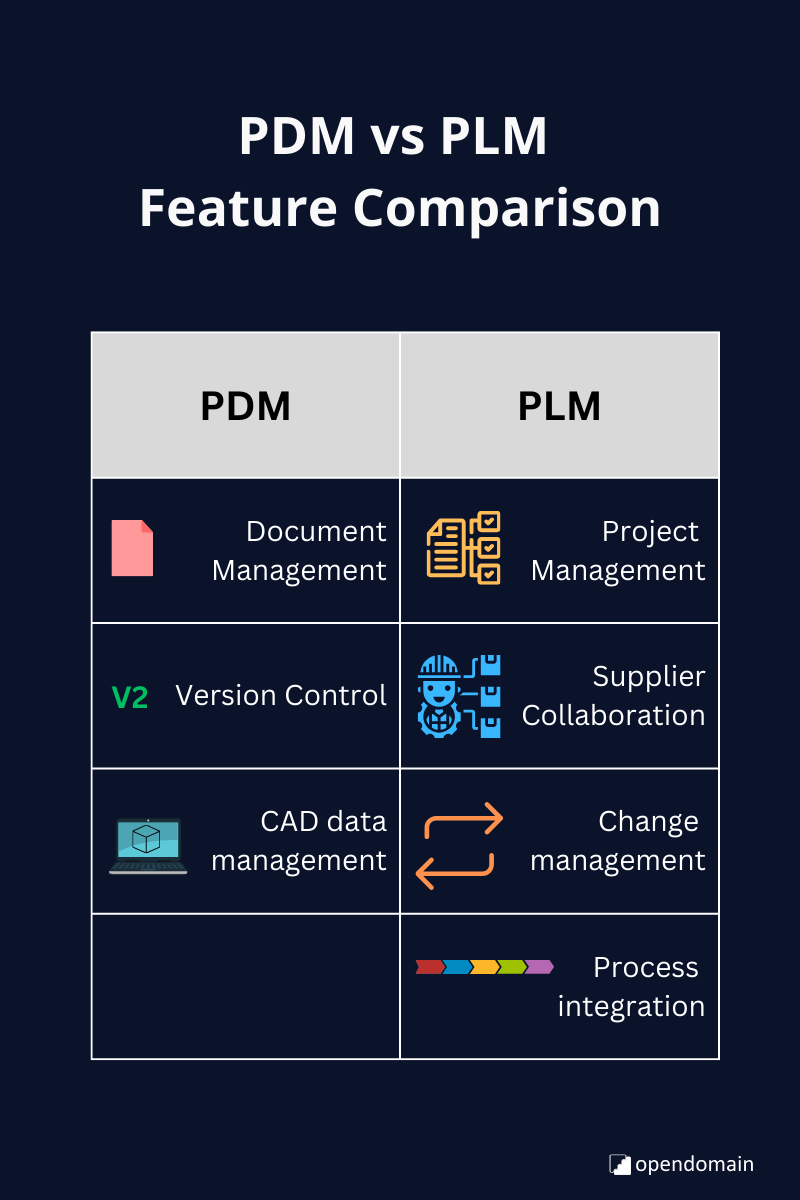
Which solution is for you?
Here are a couple of important questions to ask yourself.
1. What problems are you experiencing in your workflow?
What types of problems are you and your team experiencing during the product creation process? Are they problems with finding and managing files? What types of files? Just engineering files?
If you are experiencing major issues with CAD files and engineering design, then consider PDM software. If you are experiencing issues with more than just CAD files, then consider PLM.
2. Where is the bottleneck?
Where is the bottleneck of your process? Solving for the bottleneck can be a good place to start to effectively improve overall efficiency. A bottleneck in your process is the stage at which the total flow of production slows down. As if a four lane highway suddenly turned into a one lane highway. Traffic would occur and frustration would unleash. In business, it might not be as obvious. We are all working on our own tasks and you might not have enough information to understand where the bottleneck truly lies. Consider analyzing and investigating where your bottleneck truly lies. If the bottleneck lies in manufacturing, then improving engineering design won’t truly help solve efficiency issues. If your bottleneck lies in engineering and design, a PDM solution could help improve your efficiency. If it lies elsewhere along the product creation process, consider a PLM solution.
3. What is your budget?
Implementing a larger system like a PLM system can take more effort and cost more. How much time are you willing to put in to implement a PLM system? How much budget does your team have for implementing such a system? These key questions can help you determine if you should start with a PDM system or undertake a larger PLM system implementation.
Starting small
PLM is a bigger undertaking than starting with a PDM. If you truly don’t know where to start, start small. There is a lot of intersection between PDM and PLM systems. Some PDM systems have morphed into PLM systems, but still offer PDM solutions. Some PDM systems offer PLM add-ons to help your team grow when they are ready.
Conclusion
PDM and PLM can be confusing at first, but with a little more research and understanding, it can be helpful to understand what these terms mean and how they relate to your business. These systems were built because many people identified problems with the product creation process. There are key differences such as size and scope, integrations, purpose, and budget. Consider analyzing efficiencies and inefficiencies of your process before identifying which problem you are trying to solve so you can understand which is right for you, PDM or PLM.
Share:
.svg)